Overview
I collaborated with a group to design a linkage system capable of translating rotary motion of a motor into linear motion for pressing a button. Our primary bjective was to optimize the duration of button pressing, while also considering geometric constraints, material properties, loading conditions, and workspace limitations.
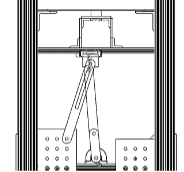
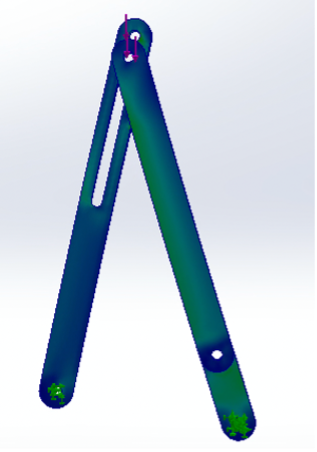
Design and Analysis Process
My team began the design brainstorming process by drawing inspiration from the crank rocker mechanism. We counsidered various mounting positions and link lengths, as well as experimented with incorporating slotted portions. After thorough consideration, we opted for a design featuring a slotted link, anticipating that it would enable the system to maintain a vertical position for an extended duration. Using Solidworks, my group members and I generated models and conducted motion simulations of our designs, allowing us to select the one which would yield the longest button pressing time. Finally, we performed Finite Element Analysis (FEA) simulations and conducted hand calculations to size our links.
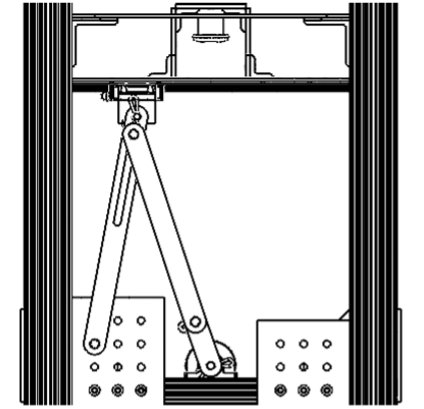
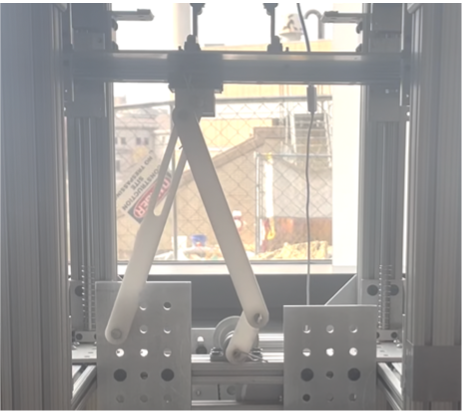
Iteration Process
On the first testing day, our assembly successfully pressed the button without experiencing any failures or causing the motor to stall. However, we encountered an issue with the slot mechanism, which resulted in the system descending sooner and more rapidly than anticipated. As a result, the button was only pressed for a total of 3 seconds during a 2-minute period. We then refined our design using our understanding of Grashof’s criterion, as well as insights gained from testing. This involved elongating two of our links and repositioning the assembly mounting position. Despite our doubts regarding the functionality of the slot due to friction, we opted to keep it in our design to minimize system weight. We then repeated the analysis process.
Results
During the final testing day, the system exhibited a gradual and steady descent without any sudden drops. Our assembly was able to successfully press the button for over 41 seconds within the 2-minute timeframe, marking a significant improvement of 38 seconds in button press time. This project demonstrated the importance of iteration for continuous improvement in the design process. Through this experience, I learned how to use Solidworks motion simulations to visualize assembly behavior.